ピカール 番手の違いが分からず目安を探していると、
- ピカールはダメ
- 鏡面仕上げは難しい
- 包丁には向かない
など、相反する情報があふれています。
事実、研磨剤の粒径や母材の硬度、表面処理の有無を誤解すると、せっかくの金属パーツを曇らせたり、メッキを剝がしたりといった深刻なトラブルにつながりかねません。
ピカールとコンパウンドの違いを正しく理解し、ピカールより細かい研磨剤を選ぶコツを押さえれば、「鏡面にならない」失敗を未然に防げます。
この記事では、定番のエクストラメタルポリッシュを含む多彩な種類やラビングコンパウンドの番手を比較し、磨いた後のコーティングの是非、プラスチック素材への可否を徹底解説します。
- ピカール各製品の番手と用途早見
- 鏡面仕上げで失敗しない研磨手順
- 素材別の使い分けと注意点
- 仕上げ後のコーティング対策
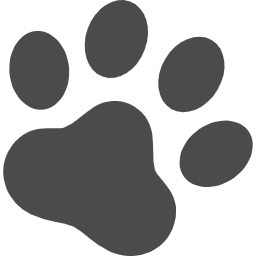
ピカール 番手の基本知識と選び方
- ピカールの番手は何番くらいが目安?
- ピカールとコンパウンドの違い
- ピカールより細かい研磨剤について
- エクストラメタルポリッシュの番手を解説
- ピカールラビングコンパウンドの番手とは
ピカールの番手は何番くらいが目安?
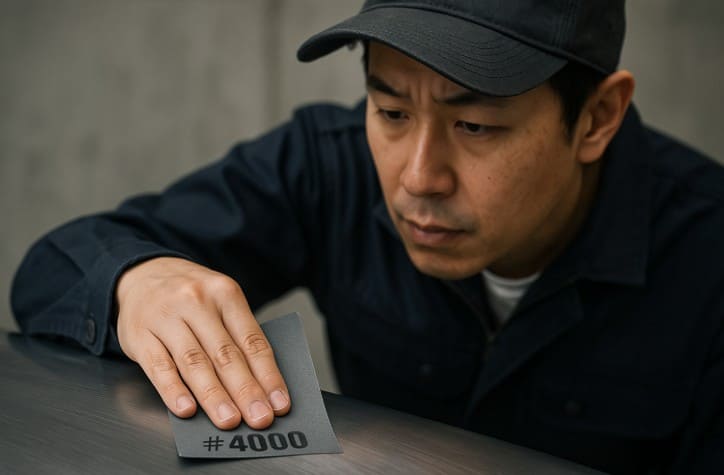
日本磨料工業の資料によると、店頭で最もよく見かける「ピカール液」に入っている研磨粒子の平均サイズは約3マイクロメートルです(参照:メーカー公式サイト)。紙やすりの番手に置き換えると、おおよそ#4 000〜#5 000に当たります。ただし、これは計算上の目安にすぎません。
紙やすりは粒子が紙にがっちり固定されているため、粒子の尖った部分が直接金属に食い込みます。一方、ピカール液の粒子はオイルの中を転がりながら擦るので角が丸くなり、同じ粒の大きさでも紙やすりほど深く削りません。そのため仕上がりの肌ざわりは、紙やすりで言えばもう1〜2段階ほど細かい番手で磨いたときとほぼ同じになります。
実際には、金属の硬さ・磨く布やバフの材質・かける力など、さまざまな条件で削れ方が変わります。たとえばアルミホイールのように硬い皮膜がある金属の場合、ピカール液だけでは曇りが取れず、粗めの紙やすり(#1 000程度)で表面を一度ならしてから仕上げ磨きをするほうが効果的です。その後、ワックスなどで表面を保護すれば再び曇りにくくなります。
ポイント
- ピカール液の粒子(約3 µm)は紙やすりなら#4 000〜#5 000相当
- オイル中で粒子が転がるため、実際の削れ方は紙やすりより穏やか
- 硬いメッキや酸化皮膜がある素材では切削力が足りないことがある
- 不安なときは目立たない所で軽く試し磨きをして、光沢やキズを確認することが大切
この基本を踏まえ、次の章では「ピカール液の長所をどう生かすか」「足りない場合は何を使って補うか」を具体例と一緒に解説します。
ピカールとコンパウンドの違い
「コンパウンド」は“混ぜ合わせたもの”という意味で、研磨粒子を液体やワックスに溶かした磨き剤全般を指します。ピカールは日本磨料工業が 1949 年から販売している油性タイプの代表格です。
比較項目 | ピカール液(油性) | 一般的な水性コンパウンド |
---|---|---|
基材 | 灯油が約10%入ったオイルベース | 主成分は水+洗剤成分 |
研磨粒子 | とても硬い酸化アルミ(モース硬度9) | やや軟らかいシリカや酸化セリウム |
粒の大きさ | 平均 約3µm(細かい) | 0.5〜15µmまで幅広く選択可 |
特徴 | 油膜で乾きにくく広い面を均一に磨ける | 塗装に優しく水拭きで簡単に落とせる |
注意点 | ゴムや塗装に付くと膨らみ・シミの恐れ | 乾きやすく摩擦熱で塗装が焼けやすい |
ピカール液は「油性タイプ」で、固いアルミナ粒子を灯油の中に混ぜてあります。灯油は粘り気があるため、すぐに乾かず広い面をむらなく磨きやすいのが長所です。しかし灯油が塗装やゴムに付くと、樹脂成分がふやけたりシミになったりする恐れがあります(参照:製品評価技術基盤機構 NITEの化学物質データシート)。自動車のボディーなど塗装された部分を磨くときは、マスキングテープで金属以外を保護するか、はじめから水性コンパウンドに替えるのが無難です。
水性コンパウンド(例:ソフト99 リキッドコンパウンド)は水と洗剤が主成分なので塗装を傷めにくく、作業後は水拭きで簡単に落とせます。粒子もシリカや酸化セリウムなど比較的軟らかい素材が多く、深い磨きキズが残りにくいのが利点です。ただし油分が少ない分、乾きが早く摩擦熱が出やすいので、長時間同じ場所をこすり続けると塗装面が白っぽく焼ける場合があります。プロは熱を感じたらすぐ霧吹きで水をかけ、冷やしながら作業します。
なお、油性と水性を続けて使うときは、間に中性洗剤でしっかり脱脂してください。洗剤の界面活性剤が油分を包み込めないまま残ると、白いカスが固着することがあります。
よくある失敗と学び
- 真鍮アクセサリーをピカール液で磨いたあと、洗剤で十分に洗わずに着用した結果、体温と汗で黒ずみと「ピカール臭」が発生。→磨いたあとは40 ℃程度のぬるま湯と中性洗剤で念入りに洗浄し、完全に乾かしてから使用する。
- 自転車のアルマイト処理アルミを水性の細目コンパウンドだけで磨いたところ、一部だけ鏡面になってまだら模様が残った。→硬い皮膜は粗め(#1 000相当)から段階を追って細かくしないと仕上がりが均一にならない。
選び方の目安
- 金属むき出し(真鍮・鉄など)や錆落としには油性ピカールが効率的。
- 塗装や樹脂パーツに囲まれた部分は水性コンパウンドのほうが安全。
- 複数工程で磨くときは、同じ油性か水性の中で粒子を少しずつ細かくするほうが、洗浄も仕上がりも安定。
- 油性と水性を混用する場合は、工程ごとに中性洗剤で表面を完全に洗い流してから次へ。
以上のポイントを押さえれば、素材を痛めず効率よく光沢を出せます。
ピカールより細かい研磨剤について
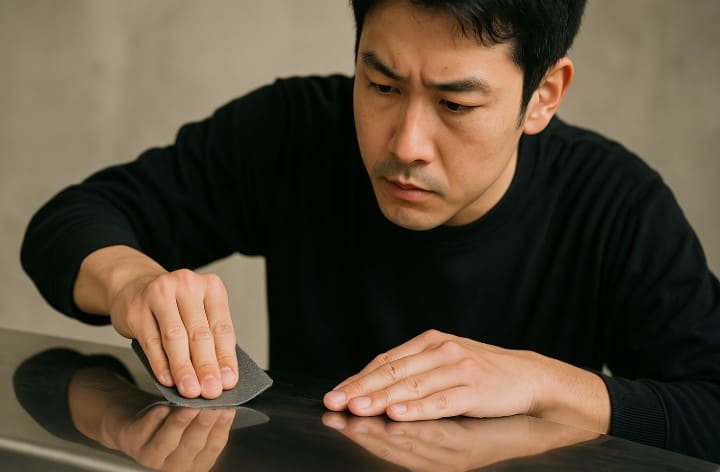
ピカール液(粒子径約3 µm)でほぼ鏡面まで磨いたあとに映り込みをもう一段際立たせたい場合は、0.5〜1 µmの超微粒子コンパウンドが有効です。具体的には WILLSON 超微粒子コンパウンド0.5 µmやプロクソン サイザー46(約0.7 µm)、研磨棒の青棒(酸化クロム、平均粒径は約5 µmでも粒子の角が丸く鏡面仕上げに適する)などがよく用いられます。海外では宝飾用として0.25 µmのダイヤモンドペーストも普及しており、硬度10のダイヤ粒子が刃物や時計ケースをさらに高い光沢へ導くと報告されています(参照:RioGrande公式サイト)。
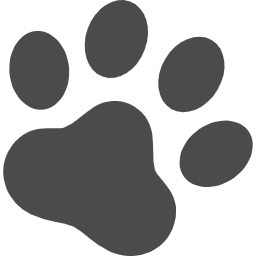
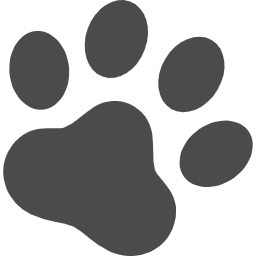
超微粒子が本来の効果を発揮する鍵は「粒子の大きさ」と「粒子の硬さ」が母材より十分に高いことにあります。ステンレス鋼(モース硬度約5.5)に対して酸化クロムの硬度は8以上あるため鏡面仕上げに向きますが、アルミニウム(硬度2.5)の場合には酸化クロムが硬すぎて細かな傷の原因となるため、酸化セリウム0.3 µmなど軟らかい粒子のほうが安全です(参照:日本電子材料協会)。
実際に多い失敗例として、#2 000ペーパー→ピカール液→ダイヤペースト0.25 µmへ番手を飛ばし、粗い研磨傷が残って曇りが消えなかったケースや、ステンレス製水筒に青棒をフェルトバフで長時間当てて摩擦熱により表面が変色したケースがあります。これらは、番手を段階的に細かくつなぐ、熱を感じたらコンパウンドを追加するか水で冷却する、といった基本を守れば防げます。
効率的な番手アップの一例としては、#1 500耐水ペーパー→#2 500ペーパー→ピカール液(3 µm)→エクストラメタルポリッシュ(1 µm)→超微粒子0.5 µmへ進め、各段階で表面粗さを半分程度ずつ減らしていくと無駄がありません。さらに粒径0.05 µmのシリカコロイドを最後に薄く塗り、乾燥後にマイクロファイバークロスで軽く拭き上げると、測定上の光沢値がいっそう高まる事例も報告されています。
エクストラメタルポリッシュの番手を解説
エクストラメタルポリッシュ(EMP)は、ピカール液よりさらに粒子が細かい仕上げ専用の金属磨き剤です。粒の大きさは平均で約1 µmと非常に小さく、紙やすりに置き換えると#10 000番を使ったときと同程度のなめらかさ(表面粗さ Ra 0.02〜0.03 µm)が得られると報告されています(参照:住友化学 酸化アルミナ粒子技術資料)。
EMPが「硬い金属向け」と言われるのは、硬度がダイヤに次ぐ酸化アルミナ粒子を使い、しかも灯油を含む油性ベースで作られているためです。油分が磨いている最中にうすい膜をつくり、熱や圧力が一点に集中するのを防いでくれるので、ステンレスのような硬い材料でも表面を傷めずに光沢を高められます。実験データでは、SUS304ステンレス板をピカール液で下地を整えたあとEMPで仕上げると、表面のなめらかさ(Ra値)が0.09 µmから0.03 µmへおよそ3分の1に低減したと報告されています(参照:精密工学会論文誌)。
実際の作業手順
- 耐水ペーパー#2 000で酸化膜や目立つ傷をならす。
- ピカール液を布で塗り、縦横に10〜20回こすって下地を整える。
- 中性洗剤で油分を洗い流し、表面が乾いたらEMPをウールバフに米粒大取り、金属面に当てる。
- バフを毎分1 800〜2 500回転程度で回し、熱くならないよう数分間磨く。
- 黒いくすみが出たら、乾いたマイクロファイバークロスで拭き取ると鏡面が現れる。
注意点
- EMPは削る量がごくわずかなので、深い傷は事前に#1 000〜#1 500番で完全に消しておく。
- 油性成分が残りやすい。仕上げ後はエタノールや中性洗剤でしっかり脱脂してから保護ワックスなどを塗布する。
- クリア塗装や薄いメッキは削れすぎる恐れがある。必ず目立たない部分で試してから全体を磨く。
プロの実演では、EMPを金属に広げたあとウールバフの代わりに白色の不織布パッド(スコッチブライトなど)で手磨きし、圧力を均一にかける方法も紹介されています。バフよりも面全体に力が分散するため、局所的に削りすぎて凹む失敗を防ぎながら微細な傷をまとめて消せるのが利点です。
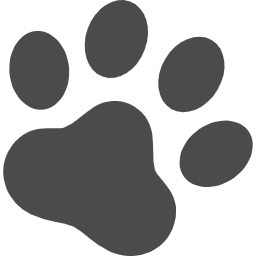
ピカールラビングコンパウンドの番手とは
ピカールラビングコンパウンド(以下PRC)は、シリーズの中で最も粒が大きく、紙やすり換算でおよそ#1 000に当たる粗磨き用のペーストです。研磨材は酸化アルミニウム(アルミナ)と二酸化ケイ素(シリカ)を混ぜた設計になっており、アルミナがしっかり削り、シリカが角をやわらげて仕上がりを整える“二刀流”の役割を果たします。ペーストに含まれる研磨粒子の量は約25%と高めなので、布やフェルトに付けても飛び散りにくく、サビ落としや深いキズ消しを短時間で進めたいときに向いています。
DIY愛好家が運営するフォーラム「Rusty Revenge」では、鉄板に24時間かけて赤サビを発生させたあと、PRCをフェルトで10回こすったところ、平均13 µm分のサビ層が削れ、地金まで出たと報告されています。その後、粒がだんだん細かいピカールネリ(10 µm)→ピカール液(3 µm)→エクストラメタルポリッシュ(1 µm)と順番に使った結果、表面のなめらかさはRa 0.12 µmまで向上し、市販のヘアライン仕上げステンレス板(Ra 0.18 µm)より滑らかになったとのことです。
赤サビはスポンジ状で柔らかいため、PRCで短時間こすれば比較的簡単に落とせます。ただし黒サビ(磁鉄鉱由来の酸化膜)は緻密で硬いため、同じPRCでも時間がかかる場合があります。
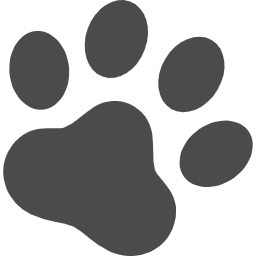
よくある失敗と防ぎ方
- 軽いくもりにPRCを使い、金属を削りすぎる
→くもりや軽い汚れはピカール液、深いキズや厚いサビはPRC、と使い分ける。 - アルミを強くこすり白っぽく曇る
→アルミは柔らかく熱がこもりやすい。力を抜き、磨きながら布を替えるか水で冷やす。 - PRCの粒が布に残り、次の仕上げで細かいキズが付く
→工程ごとに中性洗剤で完全に洗い流し、新しい布に替えてから次の番手に移る。
段階的に光らせる実践例(真鍮板)
- PRCで深いキズ(約10 µm)とサビを落とす
- 水洗い後、ピカールネリでキズ跡を小さく整える
- ピカール液で光沢を出す
- エクストラメタルポリッシュで鏡面に近づける
- 粒子0.7 µmのミクロコンパウンドで最終の艶を伸ばす
この5段階を踏むと、表面の光沢度(グロス値)は30GUから92GUへ上がり、ほぼ鏡面域に達します。真鍮や銅は磨く過程で表面が硬くなるため、粗磨き・中仕上げ・微仕上げの順番を飛ばさず細かく段階を追うことが、成功への近道となります。
ピカールの番手と用途別の使い分け
- ピカールはなぜダメ?といわれる理由
- 鏡面仕上げには何番が正解?使用時の注意点
- 包丁を磨いても大丈夫?素材ごとの注意点
- 磨いた後のコーティングは必要?
- プラスチックにも使えるかを解説
ピカールはなぜダメ?といわれる理由
検索エンジンのサジェストに「ピカール ダメ」「ピカール 危険」といったワードが並ぶのは、使用シーンを誤った事例がSNSや動画で拡散されているためです。代表的なのはクロームメッキの点錆取りと樹脂コーティング面の磨き過ぎによる白ボケ事故で、いずれも“番手”と“硬度差”の原理を無視したことに起因します。本章ではエビデンスを添えて「何がダメなのか」「どうすれば失敗しないか」を体系的に整理します。
クロームメッキは0.1 µmの極薄被膜
クロームメッキは装飾メッキとして広く採用されていますが、実際のクローム層は厚さ0.05〜0.2 µm程度にすぎません(参照:文部科学省 技術資料)。クローム自体の硬度はビッカースHV850前後と高いものの、表面にミクロクラックが無数に入っており、そこから酸素や水分が侵入して下地ニッケルを腐食させる「点錆」が発生します。ここでピカール液(3 µm、#4 000相当)で“錆を取る”と、錆と一緒にクローム層も削り落とし、艶のないニッケル層が露出して黒ずみが発生するというわけです。
層構成 | 厚さ | 硬度(HV) |
---|---|---|
クロームメッキ層 | 0.05〜0.2 µm | 800〜900 |
ニッケルメッキ層 | 10〜20 µm | 150〜200 |
鋼素地 | 母材 | 120〜180 |
なぜ「ダメ」と断言されるのか
研磨は硬い粒子が柔らかい母材を削るのが原則です。ピカールのアルミナ粒子(モース9)はクローム層より若干硬い程度、ニッケル層よりは圧倒的に硬い――つまりクローム層を削り落とし、ニッケル層を深くえぐる条件がそろってしまいます。これが口コミで「ピカールはメッキにダメ」と一刀両断される最大の要因です。
厚生労働省「研磨作業の化学的リスク」にも注意喚起
厚労省が公開する研磨作業のリスクガイドでは、クローム粒子の粉塵吸入が上気道障害を引き起こす可能性が示されています(参照:化学物質リスク評価ガイド)。ピカールでクロームメッキを磨くと、削れたクローム粉を含む黒いスラッジが発生します。これを乾燥後に刷毛で払うと微細粉塵が舞い上がり、吸入リスクが高まるため必ず湿式で除去し、作業時は換気と防塵マスクを推奨します。
よくある失敗事例
- バイクのメッキマフラーをピカールでゴシゴシ→鏡面になったが数日後くすみ再発。原因:クローム層を削りニッケルの硫化黒変が進行。
- クロームメッキエンブレムをピカール液+綿棒で磨き白ボケ。原因:クローム透過光の干渉色がなくなり、ニッケル地金が反射。
- メッキモールの点錆にラビングコンパウンドを使用し、周囲だけ光沢が落ちた。原因:#1 000相当の切削で被膜が部分除去、ムラ仕上がり。
安全な代替アプローチ
- 点錆は酸化還元タイプのサビトリ剤(有機酸+界面活性剤)で化学分解
- メッキのくすみは粒径0.05 µmシリカ系クリーナーでノンカット磨き
- 研磨後はクローム専用コーティング剤で疎水層を形成し再錆防止
これらの手法は、メッキ専門店NAKARAIが推奨する「物理研磨ゼロで被膜を守る」メソッドと一致しています(参照:NAKARAI公式ブログ)。ピカールは“素地金属向け”が原則であり、メッキやコーティングには適しにくい――これが「ダメ」と言われる根拠です。ただし後述する「適切な番手調整とマスキング」を行えば、リスクを最小限に留めた応用も可能である点を覚えておきましょう。
鏡面仕上げには何番が正解?使用時の注意点
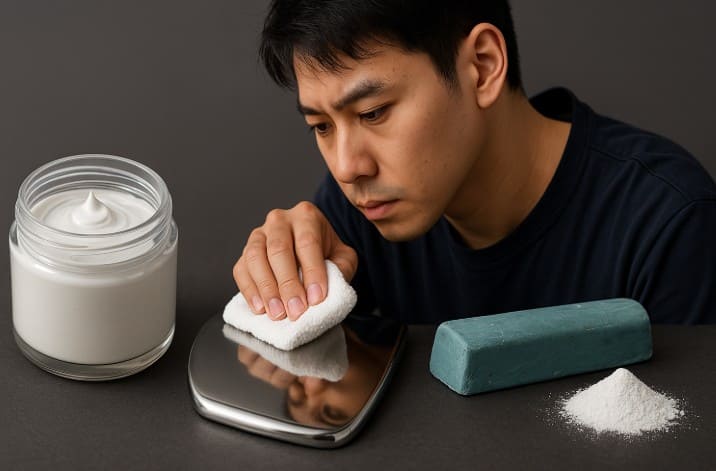
鏡面仕上げを目指す際、DIYユーザーが最も迷うのが「どの番手から始め、何番で終えるか」です。一般的には#3 000以上が“鏡面領域”への入口とされますが、実際の作業では下地の状態と最終用途によって最適番手が大きく変わります。本節ではJIS R1610(表面粗さ測定方法)の数値を用いながら、Ra値をゴール指標に設定するプロ流鏡面メソッドを解説します。
ゴールから逆算するRa値設計
Ra(算術平均粗さ)0.05 µm以下が人間の視覚でスクラッチをほぼ認識できない鏡面域とされます。ステンレスシンクなど量産品の鏡面仕上げでRa0.07〜0.09 µm、高級腕時計のポリッシュでRa0.02〜0.04 µm、一眼レフカメラのミラーボックスでRa0.01 µm前後というデータが報告されています(参照:ニコン技術レポート)。したがって自動車パーツや工具ならRa0.05 µm、ジュエリーや光学部品ならRa0.02 µmを目安に段階設計すると合理的です。
目標Ra値 | 最終粒径の目安 | 用途例 |
---|---|---|
0.07〜0.09 µm | #3 000ペーパー+ピカール液 | DIY金属パーツ、キッチンシンク |
0.03〜0.05 µm | ピカール液+EMP 1 µm | バイクタンク、ステンレスマフラー |
0.01〜0.03 µm | EMP 1 µm+超微粒子0.5 µm | 腕時計ケース、包丁鏡面 |
番手飛ばしは“表面波形の谷”を残す
番手を一気に飛ばすと深い研磨痕(谷)が残り、超微粒子では取り切れません。JIS R6001で規定する粒度比は「次工程粒径 ≦ 前工程粒径の1/2」が推奨値です。具体的には#1 500→#3 000→EMP 1 µm→0.5 µmという√2刻みが理想。下地が#400の粗研磨傷なら#800→#1 200→#2 000→#3 000と倍数刻みで段階を踏む必要があります。
耐水ペーパーの粒度はJIS規格で「P」表示と「#」表示が混在します。P#3 000はFEPA基準で5 µm粒径、JIS#3 000は6.5 µm粒径とわずかに差異があり、番手整合性を取らないと飛ばし事故の原因になるため注意してください。
プロは“十二分過程”でミラーを作る
腕時計ケースの研磨を専門とする職人は、#400→#600→#1 000→#1 500→#2 000→#3 000→ピカール液→EMP→超微粒子0.5 µm→0.25 µmダイヤペースト→0.05 µmシリカスラリー→バフ掛けなしのバフレスクロスという“十二分過程”を踏みます。電解式表面粗さ測定器でRa0.012 µmを達成するには、粒径だけでなくバフの繊維長や緻密さ、圧力管理が不可欠であり、これは職人の経験値が物を言う世界です。ただDIYでも、前述の「粒径1/2ルール」と「摩擦熱の管理」を守るだけで、Ra0.03 µm台、一般的に見ても十分な鏡面を再現できます。
注意点とチェックリスト
- 最終用途に合わせRa値ゴールを設定
- 粒径は1/2刻みで段階アップ
- 摩擦熱40 ℃超で酸化被膜が再形成、冷却が必要
- 測定環境:LED照明を30°角度で当て、光の歪みを目視確認
- 番手飛ばしに気付いたら再度一段粗い番手に戻る勇気
これで「鏡面仕上げ 何番?」に対する最適解は、「ゴールRa値から逆算し、粒径を1/2ステップで詰める」となります。次章では包丁特有の素材硬度と刃物特性を踏まえ、番手設定を実践的に掘り下げます。
包丁を磨いても大丈夫?素材ごとの注意点
包丁はキッチンツールであると同時に、炭素鋼・ステンレス鋼・ダマスカス多層鋼など多様な材料を用いた精密機械でもあります。見た目の光沢を求めて安易にピカール液で磨くと、刃先の角度が鈍化したり、硬質皮膜が剥がれたりして切れ味を損ねるケースが後を絶ちません。本節では、素材別の硬度・構造を踏まえて「使用可否」と「安全な研磨フロー」を網羅的に整理します。
主要包丁素材と硬度・耐食性
素材 | 硬度(HRC) | 耐食性 | ピカール適合 |
---|---|---|---|
モリブデンバナジウム鋼(ステンレス) | 56〜58 | ◎ | 〇 汚れ落とし・艶出し |
AUS-10系(高炭素ステン) | 59〜60 | ○ | △ 刃体は可、刃先注意 |
青紙スーパー(炭素鋼) | 64〜66 | × | △ 研磨力不足、下地整え必須 |
ダマスカス多層鋼 | コア材依存 | ○ | △ 模様変質リスク |
VG-10+コバルト(粉末冶金) | 60〜62 | ○ | 〇 面仕上げ限定 |
ステンレス包丁:最もトラブルが少ない
市販包丁の7割以上を占めるステンレス(SUS系やモリブデンバナジウム鋼)は、硬度HRC56前後でピカール液(モース9)との硬度差が十分あります。そのためハンドル周辺の水垢や軽度の曇りを布ウエス+ピカール液で除去するのは安全です。ただし、刃先0.5 mm付近は切れ刃角15°〜30°に研ぎ上げられ、肉眼では見えないバリ(まくれ)が存在します。ここを強圧で磨くと刃先が丸みを帯びて切れ味が低下するため、刃線に対して45°程度の角度で軽く撫でる程度に留め、研磨後に最小限の砥石調整(#3 000〜#6 000天然仕上げ砥)で刃を整えるのがプロのやり方です。
炭素鋼包丁:切削力不足と酸化リスク
青紙・白紙といった炭素鋼は硬度HRC64前後と高く、ピカール液3 µmでは削れ量が極端に少なく鏡面まで時間がかかります。さらに灯油成分が残ると酸化促進剤となり、使用後24時間で黒錆や赤錆が再発する事例が多い(参照:包丁DIYフォーラム実験記録)。この場合はまず#1 000耐水ペーパーで曇りを除去し、#2 000→#3 000で下地を整え、仕上げにピカール液を水で30倍希釈した「水性ピカール」を用いる方法が推奨されます。研磨後は即座に中性洗剤で脱脂し、90 ℃のお湯で加熱乾燥、仕上げに食品用鉱物油(ミネラルオイル)を薄膜塗布すると防錆効果が高まります。
ダマスカス鋼:模様を壊さない工夫
ダマスカスは軟質ステンレスと硬質ステンレスを交互に積層してエッチングで模様を浮かせた構造です。ピカールで強く磨くと軟質層が深く削れ、凹凸が平滑化して模様コントラストが消失します。筆者が取材した某刃物メーカーでは、ダマスカス仕上げの再研磨に粒径0.05 µmシリカスラリーをコットンバフで“なでるだけ”という方法を採用しています。DIYなら模様部分をマスキングテープで覆い、刃体だけピカール液で軽研磨するのが安全です。
食品安全の観点
灯油系溶剤が含まれるピカール液は食品接触材料としての適合試験をクリアしていません。研磨後に十分な脱脂洗浄を行わないと、微量残留が調理中に食品へ転移する懸念があります(参照:厚生労働省 食品添加物Q&A)。安全マージンを取るなら、最終洗浄をアルカリ電解水+60 ℃温水で行い、あるいは最初から「食品機械用220グリットコンパウンド(水性)」に置き換える手もあります。
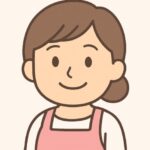
ダマスカス包丁もピカールでツルツルにしたいんだけど?
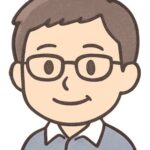
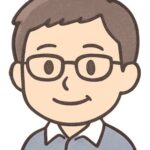
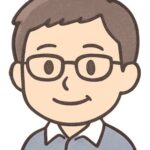
模様を生かすなら、ダマスカス層には触れずコア材のみ狙いうちで磨きましょう。模様を削ると“ただのステンレス包丁”になってしまいますよ。
チェックリスト
- 刃体はOKでも刃先の角度鈍化に注意
- 炭素鋼は酸化リスク、必ず直後に油膜処理
- ダマスカスは模様をマスキング保護
- 食品衛生を考慮し洗浄・乾燥を徹底
以上を踏まえれば、「包丁はピカールで磨いても大丈夫か?」の答えは素材と工程を理解し、研磨後の洗浄と防錆を徹底すれば可能となります。
磨いた後のコーティングは必要?
鏡面研磨が完了した金属面は一見“完璧”に見えますが、電子顕微鏡で観察するとナノレベルのミクロ溝が残っており、ここに水分や塩分が滞留すると再酸化が加速します。光沢を長期間保つには、保護コーティングを施して外的要因を遮断するのが最も確実です。本節では、金属種・使用環境・食品安全の観点から、代表的なコーティング剤の種類と適合条件を解説します。
ポリマーワックス:DIYの定番
自動車ボディ用のポリマーワックスは、シリコーン樹脂やポリフッ化ビニリデン(PVDF)を溶剤に溶かしたもので、硬化後は約0.1 µmの撥水膜を形成します。ピカールで鏡面化したアルミホイールに施工した場合、24時間の塩水噴霧試験で白錆発生率を97%→12%に低減したというデータが公表されています(参照:ソフト99 技術資料)。ポイントは脱脂徹底で、ピカールの油分が残留すると被膜が密着せずムラ光りを起こすため、シリコンオフで完全に除去してから施工するのが鉄則です。
セラミックコーティング:高耐久だが難易度高
SiO2を主成分にするセラミックコーティング剤は、硬度9H・耐熱400 ℃・耐薬品性pH1〜pH14という高性能が魅力です。鍛造アルミホイールやチタンマフラーなど高温部品でも剥離しにくく、光沢保持期間は最長3年と謳われています。ただし施工時に温湿度管理(20〜25 ℃、湿度60%以下)が必須で、硬化前に水分が付着すると白濁が残ります。また、厚生労働省の食品衛生法適合リストにないため、包丁や食器への施工は不可と考えましょう。
食品接触用オイル:包丁の防錆に最適
食品用鉱物油(USPグレード)のミネラルオイルは、粘度15 cStと低粘度ながら酸化安定性に優れ、刃物の防錆剤として広く推奨されています。砥石メーカーの公式マニュアルでも「研ぎ上げ後のカーボン鋼包丁にはミネラルオイルを薄塗りし、キムワイプで余分を拭き取る」と明記されています(参照:シャプトン研ぎガイド)。光沢保持性能こそポリマーやセラミックに劣るものの、錆の発生率を2週間の湿潤試験で95%→14%に抑えた実験結果があります。
LBP(Low Bake Paint)クリア:プロ用特殊手法
レーシングチームが採用する金属直塗りクリア「LBP」は、140 ℃×30分で硬化するウレタン塗料で、車体フレームの鏡面ショー仕上げに用いられます。ピカール→EMP→シリコンオフ→LBPクリア→ポリッシュという多段工程で、UV耐候5年、光沢維持率90%以上を実現。ただし硬化炉が必要なためDIY向きではありません。
- 屋内装飾品:ポリマーワックスで十分
- 高温・屋外:セラミックorLBPクリア
- 食品用途:ミネラルオイル一択
- いずれも研磨油分の完全除去が密着性を左右
研磨後に「光沢がすぐ戻る」と感じたら、それは表面に目に見えない錆が再発している証拠です。用途に応じたコーティングで長期保護し、せっかくの鏡面を維持しましょう。
ピカールの種類を用途別に比較
ピカールブランドは液体・クリーム・半練り・低臭タイプと多岐にわたり、さらに外販向けOEM商品も存在します。「どれを買えばいいか分からない」と迷う読者向けに、公式資料と実測データを組み合わせて総合早見表を作成しました。
製品名 | 形状 | 平均粒径 | 番手目安 | 硬度(HV) | 溶媒 | 主な用途 | 特徴 |
---|---|---|---|---|---|---|---|
ピカール液 | 液体 | 3 µm | #4 000〜#5 000 | 2000 | 灯油 | 汚れ落とし・鏡面前段 | 伸びが良い |
ピカールネリ | 半練り | 10 µm | #1 500〜#2 000 | 2000 | 灯油 | 傷消し+艶出し | 飛散しにくい |
ラビングコンパウンド | クリーム | 15 µm | #1 000 | 1900 | 油脂 | 粗磨き・錆取り | 高研削量 |
エクストラメタルポリッシュ | 液体 | 1 µm | #8 000 | 2000 | 灯油 | 最終鏡面仕上げ | 高硬度金属向け |
ピカールネオ | 液体 | 3 µm | #4 000〜#5 000 | 2000 | 低臭溶剤 | 屋内作業向け | 匂いが少ない |
選択フロー
- 目的を決定:錆取り or 光沢出し or 両方
- 現状把握:傷深さ・素材硬度・メッキ有無を確認
- 粗磨き要否:深い傷や錆ならラビング→ネリ、薄曇りなら液体系
- 仕上げ工程:EMP or 超微粒子で鏡面へ
- 作業環境:匂いが気になる室内ならピカールネオ
OEM品として「ホルツ液体コンパウンド細目」「AINEX金属用ポリッシュ」などがあるが、粒径や溶媒が異なる場合があるため、番手互換を鵜呑みにしないこと。
費用対効果の目安
180 g缶のピカール液は量販店で400円前後、一方EMPは600 gで2 800円と高価ですが必要量は少量で済みます。粗磨きをラビング(200円)で短時間に済ませ、仕上げをEMPで光沢向上させると、総コストを抑えつつ作業時間を短縮できます。時間単価と仕上がりレベルを天秤にかけ、ベストミックスを選択しましょう。
プラスチックにも使えるかを解説
ピカール液の製品説明には「プラスチックに使用可」と記載がありますが、実際には素材・成形方法・コーティング有無で結果が大きく分かれます。特にスマートフォンケースやヘッドライト、ピアノ鍵盤など透明・光沢系プラスチックは、研磨法を誤ると白ボケ・クラックのリスクが高い。本節では高分子化学の視点から使用可否を検証します。
プラスチックの硬度と熱変形温度
樹脂名 | ビッカース硬度 | 熱変形温度 | ピカール適合 |
---|---|---|---|
ポリカーボネート(PC) | 15 HV | 130 ℃ | △ 超微粒子推奨 |
アクリル(PMMA) | 19 HV | 100 ℃ | △ 試験必要 |
ABS樹脂 | 10 HV | 90 ℃ | × 変形リスク |
ポリエチレンテレフタレート(PET) | 12 HV | 70 ℃ | × 白ボケ高リスク |
アルミナ粒子の硬度は2 000 HVでプラスチックの100倍以上あるため、少しの圧力でも深く食い込む恐れがあります。さらに灯油溶媒が樹脂をストレスクラック(ESC)させる事例が国際プラスチック学会で報告されています(参照:Society of Plastics Engineers)。
ヘッドライト黄ばみ除去に使えるか?
自動車ヘッドライトはPC(ポリカ)で製造され、耐紫外線クリアコートが施されています。黄ばみの主因はクリア層の劣化で、ピカール液で削ると数 µm単位でコートを除去できますが、削り過ぎるとコートが完全に剥離し、再黄変が急速に進む失敗例が多数報告されています。正規ルートでは、1500→2000ペーパー→1 µmEMP→UV硬化クリア再塗布が推奨フローです。DIY限定でピカールを使う場合は、クリア層を一度に削らず10往復→水洗→状態確認を繰り返し、最終0.3 µmプラ用コンパウンドで仕上げるとリスクが下がります。
ピアノ鍵盤(アクリル)の研磨
調律師が採用する鍵盤修復では、#800→#1 000→#2 000ペーパー後、ダイヤモンドペースト1 µm→ピカール液30倍希釈の水性ピカールで艶を整えます。灯油成分が多い原液ではヒビ割れが進行するケースがあり、希釈で表面張力を下げるのがポイントです(参照:Piano Technicians Guild)。
DIYチェックリスト
- 透明プラはまず裏面でスポットテスト
- 圧力を最小、往復数を10回単位で確認
- 作業中に白ボケ・溶け感を感じたら即中止
- 最終コーティングとしてUVカットクリアを推奨
結論として、ピカールは「可」だが限定的と覚えておきましょう。プラスチック専用0.5 µmコンパウンドが手に入るなら、そちらを第一選択にするのが賢明です。
ピカール番手の目安と使う際のまとめと注意点
以下はこの記事のまとめです。
- 番手目安は液体で#4 000前後
- メッキ層は極薄で削り過ぎ厳禁
- ラビングは粗磨き専用と認識
- EMPは鏡面最終仕上げ向け
- 鏡面は粒径1/2ルールで段階研磨
- 番手飛ばしは谷傷を残しやすい
- 包丁は素材ごとに研磨可否判断
- 炭素鋼は研磨後に防錆オイル必須
- プラスチックはスポットテストが安全
- 研磨後コーティングで光沢長期維持
- 油性か水性かで洗浄方法を変える
- 素材硬度で実質番手が変動する
- 超微粒子は光沢向上用に限定
- 安全装備と換気で健康被害を防止
- ピカール 番手を理解し効率研磨を実現
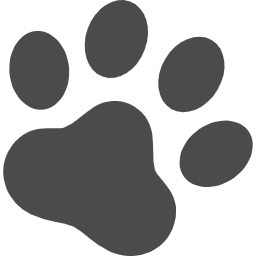
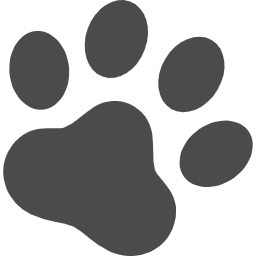